OZVER MEKATRONIK
ماشین های OZVER:
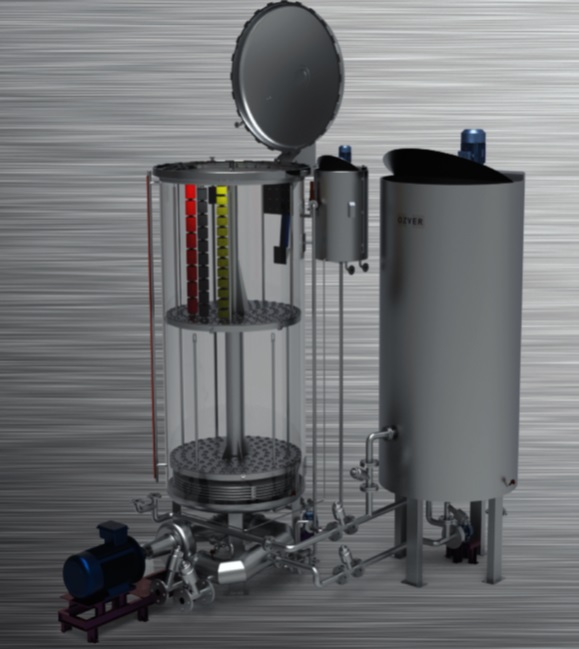
CONE DYEING MACHINE
It is designed for bleaching, dyeing, and washing processes of all kinds of polyester, cotton, and acrylic derivative materials with different carrier systems and air cushion systems in the form of coils, fibers, tops, etc. with minimum liquor ratios.
World’s largest capacity with loading up to 4000 kg in the polyester bobbin and staple fiber. The largest capacity in the world with loading up to 2500 kg in cotton and its byproducts.
ADVANTAGES
• Loading capacities range from 20 to 4000 kg.
• It is possible to dye up to 3 kg of polyester (1,800 g of cotton) coils without difficulty.
• Main scroll pump and fan are made of AISI 316L sheet metal.
• With its powerful main pump, it allows for hassle-free dying even on the most challenging items.
• With the alternator system, it is possible to work inside-outside and outside-inside without halting the main pump.
• Low liquor ratio 1:4 / 1:6 with its advanced design and air cushion system.
• Low process times with its advanced design.
• Working capacity ranges from 50% to 100%, depending on the situation.
• The serpentine inside the boiler ensures high-efficiency heating and cooling.
• Three-stage pump provides high-efficiency dosing.
• With an advanced automation system, it’s simple to use and repeat processes.
• In comparison to standard machines, it uses less energy, steam, and water.
• Fully automatic lid-locking and carrier fixing system.
All parts that come into touch with paint, chemicals, or liquor are made of AISI 316L quali¬ty stainless steel, which is highly chemically resistant and meets European CE Norms.
High-capacity 316 L quality stainless steel centrifugal pump made of 8 mm sheet metal, mounted next to the boiler. The pump shaft is supported by two bearings and there is a self-adjusting mechanical seal with a maintenance-free spring. The pump shaft and mo¬tor shaft are connected to each other by coupling. The pump fan is manufactured from sheet metal.
It is a system that enables alternator internal-external and external-internal paint circu¬lation without stopping the pump motor. It works with a piston according to the principle that the suction mouth of the pump can intake both from inside or outside the coil.
Stainless centrifugal pump with mechanical saimstra. It is added while under pressure from the supplementary vessel to the main boiler. The injection pump manufactured with three fans is 2800 rpm. Dosing is provided from the additional cabin to the main boiler without reducing the boiler pressure during dosing.
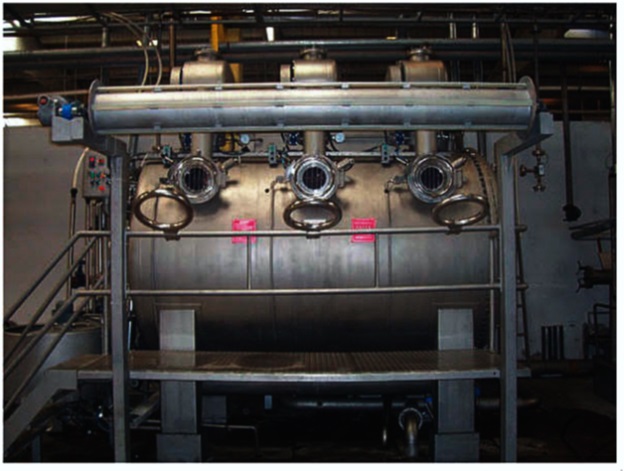
HT ROTA DYE
FABRIC DYEING MACHINE WITH ROTATING CABIN
ÖZVER ROTA-DYE HT FABRIC DYEING MACHINE
It has been produced by only two companies in the world, and it is designed for bleaching, dyeing, and washing processes of the tube and open-width fabrics far ahead of today.
It provides a high-quality dyeing guarantee for all kinds of knitted cotton, cotton lycra blends, viscose and viscose lycra blends, mat products, and towel-type fabrics.
With the rotating cabin system inside, the need for high liquor to transport the fabric in the machine is eliminated.
With the shaking group in the spinning cabin, it produces unparalleled stacking. It is the last point in fabric unshrinkability to be reached.
Filter cleaning is possible even during dyeing due to the filter on the machine’s liquor level.
With a variety of nozzles available in various diameters, working conditions are appropriate for dyeing fabrics weighing between 70 g/m and 2300 g/m.
All parts that come into touch with paint, chemicals, or liquor are made of AISI 316L quality stainless steel, which is highly chemically resistant and meets European CE Norms.
It can be manufactured in a variety of capacities, ranging from 25 kg to 1600 kg.
ADVANTAGES
• The rotating cabin ensures perfect fabric transfer from rear to front of the machine.
• Seamless fabric flow with piston-driven adjustable nozzle.
• Perfect fabric stacking thanks to the shaking in the cabin.
• Low fabric shrinkability.
• Filter cleaning possibility even during painting with separate filter system
• Seamless fabric dyeing due to the high efficiency of the main pump.
• Environmentally friendly dyeing with a low liquor ratio.
• Working with low energy costs.
• Ease of use and repeatability between processes with an advanced automation system.
• Minimizing employee errors thanks to the three-point safety cover system.
• Low energy, steam, and water consumption compared to standard machines.